Toz Metalurji (P/M) hissələrinin kəsmə emalı
Avtomobil güc sistemləri üçün hissələrin istehsalı üçün toz metallurgiya (P / M) prosesinin istifadəsi getdikcə artmaqda davam edir. P / M prosesi ilə istehsal olunan hissələr bir çox vacib və bənzərsiz üstünlüklərə malikdir. Bu hissələrdə qəsdən qalan qalıq məsaməli quruluş özünü yağlama və səs izolyasiyası üçün yaxşıdır. Ənənəvi tökmə üsulu ilə istehsalı çətin və ya qeyri -mümkün olan kompleks ərintilər P / M texnologiyasından istifadə etməklə istehsal edilə bilər. Bu texnologiya ilə istehsal olunan hissələr ümumiyyətlə çox az işləmə qabiliyyətinə malikdir və ya heç olmur ki, bu da materialları daha ucuz və daha az tullantıya çevirir. Təəssüf ki, bu xüsusiyyətlərin cazibəsinin arxasında P / M hissələrinin işlənməsi çətindir.
P / M sənayesinin orijinal niyyətlərindən biri bütün emalları aradan qaldırmaq olsa da, bu məqsədə hələ nail olunmayıb. Əksər hissələr yalnız "son formaya yaxın" ola bilər və hələ də bəzi bitirmələrə ehtiyac var.
Bununla birlikdə, döküm və döymə ilə müqayisədə, P / M hissələrindən çıxarılması lazım olan az miqdarda material, aşınmaya davamlı tipik bir materialdır.
Gözenekli quruluş, p / M hissələrinin geniş istifadəyə malik olmasını təmin edən xüsusiyyətlərdən biridir, lakin alətin ömrü də məsaməli quruluşa görə zədələnəcəkdir. Gözenekli quruluş yağ və səsi saxlaya bilir, eyni zamanda mikro aralıq kəsiklərə səbəb olur. Çuxurdan bərk hissəciklərə geri və irəli hərəkət edərkən, alət ucu davamlı olaraq təsir edir, bu da çox kiçik yorğunluq qırıq deformasiyasına və kəsici kənar boyunca incə kənarın çökməsinə səbəb ola bilər. İşi daha da pisləşdirmək üçün hissəciklər ümumiyyətlə çox çətindir. Ölçülən materialın makro sərtliyi 20 ilə 35 dərəcə arasında olsa belə, komponentin hissəcik ölçüsü 60 dərəcəyə qədərdir. Bu sərt hissəciklər ciddi və sürətli kənar aşınmasına səbəb olur. Bir çox p / M hissələri istiliklə müalicə olunur və istilik müalicəsindən sonra materialın sərtliyi və gücü daha yüksəkdir. Nəhayət, sinterləmə və istilik müalicəsi texnologiyası və istifadə olunan qazlar səbəbindən materialın səthində sərt və aşınmaya davamlı oksidlər və / və ya karbidlər olacaq.
P / M hissələrinin performansı
İşlənmə qabiliyyəti də daxil olmaqla P / M hissələrinin əksər xüsusiyyətləri yalnız ərintinin kimyəvi tərkibi ilə deyil, məsaməli quruluşun gözeneklilik səviyyəsi ilə də əlaqədardır. Bir çox struktur hissənin gözenekliliği 15% -dən 20% -ə qədərdir. Süzmə cihazları kimi istifadə olunan hissələrin gözenekliliği 50%-ə qədər ola bilər. Seriyanın digər ucunda saxta və ya itburnu hissələrinin gözenekliliyi cəmi 1% və ya daha azdır. Bu materiallar, avtomobil və təyyarə tətbiqlərində daha yüksək gücə çata bildikləri üçün xüsusi əhəmiyyət kəsb edir.
P / M ərintisinin çəkilmə gücü, sərtliyi və süniliyi sıxlığın artması ilə artacaq və işlənmə qabiliyyəti də yaxşılaşdırıla bilər, çünki gözeneklilik alət ucuna zərərlidir.
Gözeneklilik səviyyəsinin artması, hissələrin səs izolyasiya performansını artıra bilər. Standart hissələrdəki sönümləmə salınması, P / M hissələrində əhəmiyyətli dərəcədə azalır, bu dəzgahlar, kondisioner üfürücü borular və pnevmatik alətlər üçün çox vacibdir. Özünü yağlayan dişlilər üçün də yüksək gözeneklilik lazımdır.
Emalda çətinliklər
P / M sənayesinin davamlı inkişafının məqsədlərindən biri də emalın aradan qaldırılması olsa da və P / M prosesinin əsas cazibədarlıqlarından biri də az miqdarda emala ehtiyac olsa da, bir çox hissənin əldə etmək üçün hələ də sonrakı müalicəyə ehtiyacı var. daha yüksək dəqiqlik və ya daha yaxşı səth işlənməsi. Təəssüf ki, bu hissələri emal etmək olduqca çətindir. Qarşılaşılan problemlərin çoxu gözeneklilikdən qaynaqlanır. Gözeneklilik, kəsici hissənin mikro yorğunluğuna səbəb olur. Qabaqcıl tərəf daim kəsilir və çıxır. Hissəciklər və deliklər arasında keçir. Təkrarlanan kiçik zərbələr kəsici kənarında kiçik çatlar əmələ gətirir.
Bu yorğunluq çatlaqları qabaqcıl çökənə qədər böyüyür. Bu cür mikro qırılma kənarı ümumiyyətlə çox kiçikdir və ümumiyyətlə normal aşındırıcı aşınma göstərir.
Gözeneklilik, P / M hissələrinin istilik keçiriciliyini azaldır, bu da kəsici kənarda yüksək temperaturla nəticələnir və kraterin aşınmasına və deformasiyasına səbəb olur. Daxili əlaqəli gözenekli quruluş, kəsmə sahəsindən kəsici mayenin axıdılması üçün bir yol təmin edir. Bu, xüsusilə qazma işlərində isti çatlara və ya deformasiyaya səbəb ola bilər.
Daxili məsaməli quruluşun səbəb olduğu səth sahəsinin artması da istilik müalicəsi zamanı oksidləşməyə və / və ya karbonlaşmaya səbəb olur. Daha əvvəl də qeyd edildiyi kimi, bu oksidlər və karbidlər sərt və aşınmaya davamlıdır.
Gözenekli quruluş, son dərəcə vacib olan hissə sərtliyinin oxunmasının uğursuzluğunu da verir. P / M hissəsinin makro sərtliyi qəsdən ölçüldükdə, çuxur sərtliyi faktorunu ehtiva edir. Gözenekli quruluş strukturun çökməsinə gətirib çıxarır və nisbətən yumşaq hissələr haqqında yanlış təsəvvür yaradır. Hissəciklər daha çətindir. Yuxarıda təsvir edildiyi kimi, fərq dramatikdir.
PM hissələrində daxilolmaların olması da əlverişsizdir. İşləmə zamanı bu hissəciklər səthdən yuxarı çəkiləcək və alətin qarşısında sürtüləndə hissənin səthində cızıq və ya cızıq əmələ gələcək. Bu daxilolmalar, ümumiyyətlə, hissənin səthində görünən deliklər buraxaraq böyükdür.
Karbon tərkibindəki fərq, işlənmə qabiliyyətinin uyğunsuzluğuna səbəb olur. Məsələn, fc0208 ərintisinin karbon tərkibi 0.6% -dən 0.9% -ə qədərdir. 0.9% karbon tərkibli bir sıra materiallar nisbətən sərtdir və nəticədə alət ömrü zəifdir. 0.6% karbon tərkibli digər materialların əla alət ömrü var. Hər iki ərintinin icazə verilən aralığındadır.
Son emal problemi, P / M hissəsində meydana gələn kəsmə növü ilə əlaqədardır. Parça son formaya yaxın olduğu üçün kəsmə dərinliyi ümumiyyətlə çox dayazdır. Bunun üçün sərbəst kəsici kənar tələb olunur. Çipin qabağındakı yığılması tez-tez mikro çiplərə səbəb olur.
Qenerasiya texnologiyası
Bu problemləri aradan qaldırmaq üçün bir neçə texnologiya tətbiq olunur (sənayeye xas olan). Səthin məsaməli quruluşu tez -tez infiltrasiya ilə bağlanır. Adətən əlavə pulsuz kəsmə tələb olunur. Son zamanlarda tozun təmizliyini artırmaq və istilik müalicəsi zamanı oksidləri və karbidləri azaltmaq üçün hazırlanmış təkmilləşdirilmiş toz istehsal üsullarından istifadə edilmişdir.
Qapalı səth gözenekli quruluş metal (adətən mis) və ya polimer infiltrasiya ilə həyata keçirilir. İnfiltrasiyanın sürtkü kimi fəaliyyət göstərdiyi ehtimal edilir. Eksperimental məlumatların çoxu göstərir ki, əsl üstünlük səthin gözenekli quruluşunu bağlamaq və beləliklə kəsici kənarın mikro yorğunluğunun qarşısını almaqdır. Söhbətin azalması alətin ömrünü və səthini yaxşılaşdırır. İnfiltrasiyanın ən dramatik istifadəsi gözenekli quruluş bağlandıqda alət ömrünün 200% artdığını göstərir.
MNS, s, MoS2, MgSiO3 və BN kimi aşqarların alət ömrünü artırdığı bilinir. Bu aşqarlar, çiplərin iş parçasından ayrılmasını asanlaşdıraraq, çipləri qıraraq çip yığılmasının qarşısını alır və kəsici kənarı yağlayır. Əlavələrin miqdarının artırılması işlənmə qabiliyyətini artıra bilər, lakin gücü və sərtliyini azalda bilər.
Sinterləmə və istiliklə işləyən soba qazına nəzarət etmək üçün toz atomizasiya texnologiyası təmiz toz və hissələr istehsal etməyə imkan verir ki, bu da daxilolmaların və səth oksidi karbidlərinin meydana gəlməsini minimuma endirir.
Alət materialı
P / M sənayesində ən çox istifadə olunan alətlər, səthinin yaxşı işlənməsi şərtilə aşınmaya davamlı, kənar çatlamaya davamlı və çipsiz materiallardır. Bu xüsusiyyətlər hər hansı bir emal əməliyyatı üçün, xüsusən P / M hissələri üçün faydalıdır. Bu kateqoriyaya daxil olan alət materialları kub bor nitridi (CBN) alətləri, örtülməmiş və örtülmüş sermetlər və təkmilləşdirilmiş örtülmüş sinterlənmiş sementli karbidlərdir.
CBN alətləri yüksək sərtliyə və aşınma müqavimətinə görə cəlbedicidir. Bu alət uzun illər Rockwell sərtliyi 45 və daha yüksək olan polad və çuqun emalında istifadə edilmişdir. Bununla birlikdə, P / M ərintisinin bənzərsiz xüsusiyyətlərinə və mikro sərtlik ilə makro sərtliyə görə əhəmiyyətli fərqə görə, CBN alətləri Rockwell sərtliyi 25 olan P / M hissələri üçün istifadə edilə bilər. Əsas parametr hissəciklərin sərtliyidir. Hissəciklərin sərtliyi Rockwell 50 dərəcəni keçdikdə, makro sərtlik dəyərindən asılı olmayaraq CBN alətləri mövcuddur. Bu vasitələrin açıq məhdudiyyəti onların sərtlik olmamasıdır. Fasiləli kəsmə və ya yüksək gözeneklilik vəziyyətində, mənfi pahlanma və ağır honlama daxil olmaqla kənarın möhkəmləndirilməsi lazımdır. Sadə yüngül kəsmə kəsilmiş kənar ilə edilə bilər.
CBN -in təsirli olan bir neçə materialı var. Ən yaxşı sərtliyə malik olan material əsasən bütün CBN -dən ibarətdir. Mükəmməl sərtliyə malikdirlər, buna görə də kobudlaşdırmaq üçün istifadə edilə bilər. Onların məhdudiyyətləri ümumiyyətlə səthin səthi ilə bağlıdır. Əsasən aləti təşkil edən fərdi CBN hissəcikləri ilə müəyyən edilir. Hissəciklər kəsici kənarından düşdükdə, iş parçası materialının səthinə təsir edəcək. Ancaq incə hissəcik alətinin bir hissəcikdən düşməsi o qədər də ciddi deyil.
Ümumiyyətlə istifadə olunan CBN materialı yüksək miqdarda CBN və orta hissəcik ölçüsünə malikdir. CBN bitirmə bıçağı incə taxıldır və CBN tərkibi aşağıdır. Yüngül kəsmə və səth emalı tələb olunduqda və ya işlənən ərinti xüsusilə çətin olduqda ən təsirli olur.
Bir çox kəsmə tətbiqində alət ömrü material növündən asılı deyil. Başqa sözlə, hər hansı bir CBN materialı oxşar alət ömrünə nail ola bilər. Bu hallarda, material seçimi əsasən hər bir kənarın ən aşağı qiymətinə əsaslanır. Bir dəyirmi bıçaq bütün CBN üst səthinə malikdir və dörd kakma CBN bıçağından daha ucuz olan dörd və ya daha çox kəsici kənar təmin edə bilər.
P / M hissələrinin sərtliyi Rockwell 35 dərəcəsindən aşağı olduqda və hissəciklərin sərtliyi aralığa daxil olduqda, sermet adətən seçimlərdən biridir. Cermets çox çətindir, çip yığılmasını təsirli şəkildə önləyə bilər və yüksək sürətə davam edə bilir. Bundan əlavə, kermetlər hər zaman poladdan və paslanmayan poladdan yüksək sürətli və bitmiş emal üçün istifadə edildiyindən, adətən formalaşmış hissələrə yaxın uyğun ideal həndəsi yivlərə malikdir.
Bu günün sermetləri metallurgiyada mürəkkəbdir və 11 -ə qədər alaşımlı elementə malikdir. Adətən TiCN hissəciklərindən və Ni Mo yapışdırıcısından sinterlənir. TiCN, sermetlərin uğurlu istifadəsi üçün vacib olan sərtlik, çip yığma müqaviməti və kimyəvi stabillik təmin edir. Bundan əlavə, bu alətlər ümumiyyətlə yüksək yapışqan tərkibə malikdir, yəni yaxşı bir sərtliyə malikdir. Bir sözlə, P / M ərintisini effektiv şəkildə işləyən bütün xüsusiyyətlərə malikdirlər. Bir neçə növ sermet təsirlidir, tungsten karbid sinterli sementli karbid kimi, bağlayıcı tərkibi nə qədər yüksək olsa, sərtlik bir o qədər yaxşı olar.
Bilinən nisbətən yeni bir inkişaf orta temperaturlu kimyəvi buxar çöküntüsünün (mtcvd) P / M sənayesi üçün də üstünlük təmin etməsidir. Mtcvd, ənənəvi kimyəvi buxar çöküntüsünün (CVD) bütün aşınma müqavimətini və kraterin aşınma müqavimətini saxlayır, eyni zamanda sərtliyi obyektiv olaraq yaxşılaşdırır. Sərtliyin artması əsasən çatlaqların azalmasından qaynaqlanır. Kaplama yüksək temperaturda saxlanılır və sonra sobada soyudulur. Alətin otaq istiliyinə uyğun olmayan istilik genişlənməsi səbəbindən örtükdə çatlar var. Düz şüşələrdəki cızıqlara bənzər şəkildə, bu çatlar kəsici kənarın gücünü azaldır. Mtcvd -nin aşağı çökmə temperaturu çatlama tezliyinin azalmasına və kəsici kənarın daha yaxşı sərtliyinə səbəb olur.
CVD örtük və mtcvd örtük substratı eyni xüsusiyyətlərə və kənar örtüyə malik olduqda, onların sərtliyinin fərqi nümayiş etdirilə bilər. Kenar sərtliyinin tələb olunduğu tətbiqlərdə istifadə edildikdə, mtcvd örtüyünün performansı CVD örtüyündən daha yaxşıdır. Analiz yolu ilə, məsaməli quruluşa malik P / M hissələri işlənərkən kənarın sərtliyi vacibdir. Mtcvd örtük CVD örtükdən daha yaxşıdır.
Fiziki buxar çöküntüsü (PVD) örtük mtcvd və ya CVD örtükdən daha incə və aşınmaya daha az davamlıdır. Bununla birlikdə, PVD örtük tətbiq edildikdə əhəmiyyətli təsirlərə tab gətirə bilər. PVD örtük kəsmə zamanı aşındırıcı aşınma, CBN və sermetlər çox kövrəkdir və əla səth işlənməsini tələb edir.
Məsələn, C-2 sementlənmiş karbidin kəsici tərəfi fc0205-də 180 m / dəq sürətlə və 0.15 mm / dəq sürətlə işlənə bilər. 20 hissənin işlənməsindən sonra çipin yığılması mikro çökməyə səbəb ola bilər. PVD titan nitrid (TIN) örtük istifadə edildikdə, çip yığılması məhdudlaşdırılır və alət ömrü uzanır. Bu test üçün qalay örtük istifadə edildikdə, P / M hissələrinin aşındırıcı aşınma xüsusiyyətlərinin TiCN örtüklə daha təsirli olması gözlənilir. TiCN, qalayla demək olar ki, çip yığma müqavimətinə malikdir, lakin qalaydan daha çətindir və aşınmaya davamlıdır.
Gözenekli quruluş vacibdir və fc0208 ərintisinin işlənmə qabiliyyətinə təsir göstərir. Gözenekli quruluş və xüsusiyyətlər dəyişdikdə fərqli alət materialları müvafiq üstünlüklər təmin edir. Sıxlıq aşağı olduqda (6.4g/sm3), makrohardness aşağı olur. Bu vəziyyətdə, mtcvd örtülmüş sementli karbid ən yaxşı alət ömrünü təmin edir. Kəsmə kənarının mikro yorğunluğu çox vacibdir və kənarın sərtliyi çox vacibdir. Bu vəziyyətdə, yaxşı bir sərtlik sermet bıçağı maksimum alət ömrünü təmin edir.
6.8 q / sm3 sıxlıqla eyni ərintini istehsal edərkən aşındırıcı aşınma kənar çatlaqdan daha vacib olur. Bu vəziyyətdə mtcvd örtük ən yaxşı alət ömrünü təmin edir. PVD ilə örtülmüş sementli karbid iki növ son dərəcə sərt hissənin sınanması üçün istifadə olunur və kəsici kənarına toxunduqda qırılır.
Sürət artdıqda (xətti sürət dəqiqədə 300 metrdən çoxdur), kermetlər və hətta örtülmüş sermetlər krater aşınması yaradır. Kaplanmış sementli karbid, xüsusilə örtülmüş sementli karbidin qabaqcıl sərtliyi yaxşı olduqda daha uyğundur. Mtcvd örtük kobaltla zəngin olan sementlənmiş karbid üçün xüsusilə təsirlidir.
Sermetlər ən çox tornalama və darıxdırıcıda istifadə olunur. PVD ilə örtülmüş sementlənmiş karbidlər, iplərin işlənməsi üçün idealdır, çünki daha aşağı sürət və yığılmaya daha çox diqqət gözlənilir.
Xahiş edirəm yenidən yazmaq üçün bu məqalənin mənbəyini və ünvanını saxlayın:Toz Metalurji (P/M) hissələrinin kəsmə emalı
Minghe Döküm Şirkəti keyfiyyətli və yüksək performanslı Döküm Parçaları istehsalına və təmin etməyə həsr olunmuşdur (metal kalıp döküm hissələri əsasən daxildir İncə Divar Döküm,Qaynar Palatanın Die Casting,Soyuq Odası Die Casting), Dəyirmi Xidmət (Döküm Xidməti,Cnc Emalı,Kalıp hazırlama, Səthi Müalicə) .Hər hansı bir xüsusi Alüminium kalıp döküm, maqnezium və ya Zamak / sink kalıp döküm və digər döküm tələbləri bizimlə əlaqə saxlaya bilərsiniz.
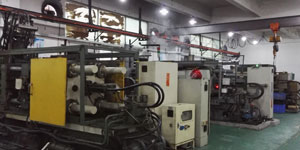
ISO9001 və TS 16949-un nəzarəti altında, bütün proseslər partlayıcıdan Ultra Sonic paltaryuyan maşınlara qədər yüzlərlə inkişaf etmiş kalıp döküm maşınları, 5 oxlu maşınlar və digər qurğular vasitəsilə həyata keçirilir. müştərinin dizaynını gerçəkləşdirmək üçün təcrübəli mühəndislər, operatorlar və müfəttişlər qrupu.
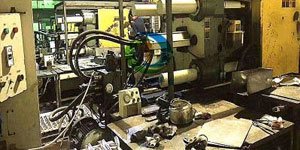
Qəlib dökümlərinin müqavilə istehsalçısı. Bacarıqlara 0.15 lbs-dən olan soyuq kameralı alüminium kalıp tökmə hissələri daxildir. 6 lbs., sürətli dəyişdirmə və işləmə. Əlavə dəyər xidmətlərinə cilalama, titrəmə, çapaq alma, atəşlə partlatma, boyama, örtük, örtük, montaj və alət daxildir. İşlənmiş materiallara 360, 380, 383 və 413 kimi ərintilər daxildir.
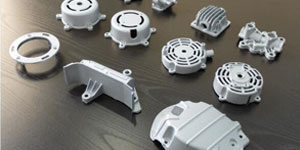
Sink kalıp döküm dizayn yardımı / paralel mühəndislik xidmətləri. Xüsusi həssas sink döküm istehsalçısı. Miniatür dökümlər, yüksək təzyiqli kalıp dökümləri, çox sürüşməli kalıp dökümləri, şərti qəlib dökümləri, bölmə kalıbı və müstəqil kalıp dökümləri və boşluq möhürlənmiş dökümlər istehsal edilə bilər. Dökümlər +/- 24 inç tolerantlıqda 0.0005 inçədək uzunluqlarda və enlərdə istehsal edilə bilər.
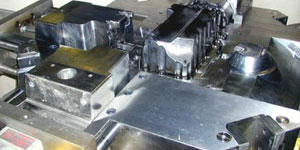
ISO 9001: 2015 sertifikalı qəlibli maqnezium istehsalçısı, İmkanlar arasında 200 ton isti kameraya və 3000 tonluq soyuq kameraya qədər yüksək təzyiqli maqnezium kalıp tökmə, alət dizaynı, cilalama, qəlibləmə, işləmə, toz və maye boyama, CMM imkanları ilə tam QA , montaj, qablaşdırma və çatdırılma.
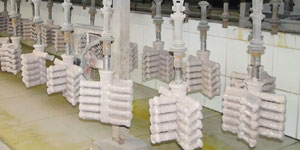
ITAF16949 sertifikatlıdır. Əlavə Döküm Xidməti daxildir investisiya döküm,qum tökmə,Ağırlıq tökmə, İtirilmiş köpük tökmə,Mərkəzdənqaçma tökmə,Vakum tökmə,Daimi kalıp tökmə, .Qabiliyyətlər arasında EDI, mühəndis yardımı, qatı modelləşdirmə və ikincil emal daxildir.
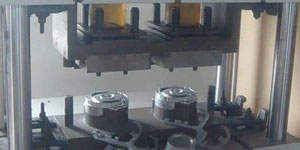
Döküm sənayesi Ehtiyat hissələri: Avtomobil, Velosiped, Təyyarə, Musiqi alətləri, Dəniz gəmisi, Optik cihazlar, Sensorlar, Modellər, Elektron cihazlar, Korpuslar, Saatlar, Maşın, Mühərriklər, Mebel, Zərgərlik məmulatları, Jigs, Telekom, İşıqlandırma, Tibbi cihazlar, Fotoqrafiya cihazları, Robotlar, Heykəltəraşlıq, Səs avadanlığı, İdman avadanlığı, Alətlər, Oyuncaqlar və s.
Bundan sonra nə etməyə kömək edə bilərik?
For Üçün Ana səhifəyə gedin Döküm Çin
→Döküm hissələri-Nə etdiklərimizi öyrənin.
→ Haqqında Ralated Tips Döküm Xidmətləri
By Minghe Die Döküm İstehsalçısı Kateqoriyalar: Faydalı məqalələr |Material Tags: Alüminium tökmə, Sink tökmə, Maqnezium tökmə, Titan tökmə, Paslanmayan poladdan tökmə, Pirinç tökmə,Bürünc tökmə,Video yayımlanır,Şirkətin tarixi,Alüminium Die Tökmə Şərhlər Off